ابزار دقیق یکی از مهمترین و کاربردی ترین زیرشاخههای مهندسی کنترل و الکترونیک بشمار میآید که در تمام صنایع، از کوچکترین کارگاهها تا بزرگترین کارخانهها و واحدهای صنعتی، نقش کلیدی ایفا میکند. اما ابزار دقیق دقیقاً چیست و چرا در فرآیندهای صنعتی و تولیدی اهمیت بسیار بالایی دارد؟
در این مقاله از آداک فرآیند سپهر، با نگاهی جامع و دقیق، به بررسی مفاهیم اساسی، اصول پایه و کاربردهای گسترده و متنوع این تجهیزات در صنایع مختلف میپردازیم و اهمیت آن را در بهبود فرآیندهای صنعتی مورد ارزیابی قرار میدهیم.
ابزار دقیق چیست؟
ابزار دقیق به وسایل و حسگرهای الکترونیکی و الکتریکی اطلاق میشود که برای کنترل و اندازهگیری دقیق کمیتهای فیزیکی و شیمیایی در فرآیندهای صنعتی بکار میروند. تجهیزات ابزار دقیق با دقت بالا و قابلیت تکرارپذیری ساخته میشوند تا اندازهگیری بصورت صحیح و قابل اعتماد انجام شود. بزبان ساده، وقتی به کلمه دقیق اشاره شد، یعنی باید اندازه گیری، کنترل و ثبت مقادیر فرایندی با دقت بالایی انجام شود.
حسگر و ترانسمیترهای هوشمند با امکانات بهتر و دقت بالا، در صنایع نفت و گاز، داروسازی و خودروسازی بطور گسترده بکار گرفته شداند. علاوه بر این، فناوریهای جدیدی مانند اینترنت اشیا (IoT) امکان نظارت و کنترل فرآیندها را از راه دور فراهم کرده و کارایی سیستمهای صنعتی را بطور چشمگیری افزایش داده است. مثلا: تشخیص مقدار دما، فشار، فلو یا جریان و چندین پارامتر دیگر و ارسال برای کنترل و مانیتورینگ آن فرسخها دورتر از محل نصب سنسور.
کار ابزار دقیق چیست؟
اساس کار تجهیزات ابزار دقیق در استفاده از حسگرها و تجهیزات برای اندازهگیری و کنترل ویژگیهای مختلف مواد (خواص فیزیکی و شیمیایی) است. این تجهیزات معمولاً اطلاعات دقیق و قابل اعتمادی از متغیرهای مورد اندازهگیری فراهم میکنند، که این اطلاعات برای تصمیمگیری و کنترل فرایندها در صنایع مختلف استفاده میشود.
یعنی استفاده از تجهیزات سنجش با دقت بالا برای اندازهگیری مقادیر مختلف فیزیکی و شیمیایی مواد. هدف اصلی این عملیات، بدست آوردن اطلاعات دقیق و قابل اعتماد از متغیرهای مورد اندازهگیری و نهایتا کنترل و ذخیزه سازی آنها است.
لیست تجهیزات ابزار دقیق کدامها هستند؟
بطور کلی دستگاههای ابزار دقیق به 9 دسته اصلی تقسیم میشوند.
- سنسورها و ترانسمیترهای اندازهگیری (دما، فشار، فلو، سطح، رطوبت، چگالی، گازها و سرعت)
- کنترلرها
- دستگاههای انتقال داده و ارتباطی
- نمایشگرها
- دیتالاگرها
- تجهیزات کالیبراسیون و تست
- شیرها و محرکها
- تجهیزات تشخیص گاز و آتش F&G و ایمنی
- تجهیزات ضد انفجاری
- نرم افزارهای مدیریت داده
سنسور و ترانسمیترهای اندازهگیری به نوبه خود ابزارهای وسیعی از این تجهیزات هستند، بررسی جدول زیر در جهت شناخت کلی این بخش ضرروری است.
انواع سنسور و ترانسمیتر ابزار دقیق
نوع اندازهگیری | انواع |
دما |
ترموکوپل – RTD – ترمیستور – ترانسمیتر دما – پایرومتر – دماسنج مادون قرمز – ترمومتر مایع در شیشه |
فشار |
مانومتر – ترانسمیتر فشار – گیج فشار – سوئیچ فشار – ترانسدیوسر فشار |
دبی |
فلومترهای مکانیکی – التراسونیک – مغناطیسی – جرمی کوریولیس – ونتوری |
تشخیص سطح |
لول گیج – لول ترانسمیتر اولتراسونیک – لول ترانسمیتر راداری – لول سوئیچ خازنی و دیاپازونی – لول ترانسمیتر دیفرانسیلی – لول سوئیچ شناوری |
رطوبت و نقطه شبنم |
رطوبت سنج خازنی، مقاومتی – ترانسمیتر رطوبت – نقطهشبنمسنج – رطوبت سنج روانسنج |
چگالی و ویسکوزیته |
دانسیمتر – ویسکوزیمتر – چگالی سنج نوری |
سرعت و ارتعاش |
تاکومتر – حسگر سرعت خطی – حسگر ارتعاش – شتاب سنج |
ترانسمیتر Transmitter
ترانسمیترها هم متغیر موردنظر را اندازه گیری میکنند و هم یک خروجی استاندارد الکتریکی مانند جریان 4 الی 20 میلی آمپری ارائه میکنند. این خروجی سپس در نمایشگر، سیستم های PLC و یا سایر ابزار های کنترلی تفسیر و از آن استفاده میشود.
کنترلر Controller
کنترلر در حقیقت یک مدار الکترونیکی است که در جهت کنترل مقادیر ورودی و خروجی استفاده میشود. کنترلر با توجه به مقادیر اندازه گیری شده، میتواند سیستم را کنترل کرده و دستورهای از پیش تعریف شده برای پیشبرد فرآیند صادر کند. مثالی بارز برای کنترلرها، میتوان به انواع PLCها اشاره نمود.
ترانسدیوسر Transducer
ترانسدیوسرها برای تبدیل مقادیر اندازه گیری شده به سیگنال الکتریکی کاربرد دارند. در حقیقت، ترانسدیوسر خود نمیتواند متغیری را اندازه گیری کند؛ بلکه صرفا برای تبدیل سیگنال کاربرد دارد. مثلا سیگنال حاصل از یک ترموکوپل را در نظر بگیرید. یک ترانسدیوسر میتواند این سیگنال را از حد میلی ولت به یک سیگنال 20mA-4 تبدیل کرده و منتقل نماید؛ اما دخالتی در امر اندازه گیری ندارد.
رکوردر Recorder & Datalogger
رکوردر یا دیتا لاگر از تجهیزات ابزار دقیق هستند که برای ذخیره اطلاعات و مقادیر اندازه گیری شده کاربرد دارند. بعبارتی دیتا لاگر (Data Logger) به دستگاهی گفته میشود که برای ذخیرهسازی دادههایی که از سنسور ها، دستگاههای اندازهگیری و سایر منابع مورد استفاده قرار میگیرند. این دستگاهها بصورت معمول با استفاده از حافظههای داخلی یا کارت حافظه(مموری)، اطلاعات را ذخیره کرده و بحالت دورهای با استفاده از روشهای انتقال داده مانند USB، Ethernet یا Wi-Fi به دستگاههای دیگر انتقال میدهند.
مثلا تصور کنید که میخواهید با ثبت مقادیر اندازه گیری شده یک ماهه توسط یک یا چند سنسور، عملکرد سیستم را بررسی کنید. در این حالت، شما به یک رکوردر نیاز خواهید داشت. از نکات بسیار مهم در انتخاب یک رکوردر تعداد ورودیها و فضای حافظه آن میباشد.
دیتا لاگرها بعنوان یکی از ابزارهای مهم در زمینههای مختلفی مانند اتوماسیون صنعتی، کنترل فرآیند، پایش محیطی و علوم پزشکی استفاده میشوند. همچنین، دیتا لاگرها برای جمعآوری و ذخیرهسازی دادههای محیطی مانند دما، رطوبت، فشار، جریان و سطح نیز استفاده میشوند.
نمایشگر Display در ابزار دقیق
همانطور که از نامشان پیداست، کار نمایشگر دریافت سیگنال الکتریکی از سنسور یا ترانسمیتر و تبدیل آنها به مقادیر قابل درک و نهایتا نمایش آنها بصورت عدد یا گرافیک است. برخی از نمایشگرها قابلیت برنامه ریزی نیز دارند که با استفاده از آنها شما قادر خواهید بود پارامترهای خاصی را تعریف کرده و با استفاده از مقادیر ورودی، امر کنترل را نیز انجام دهید.
در ادامه لیست و اسامی ابزار دقیق برحسب کاربرد را نام برده و هرکدام را شرح میدهیم. با ما همراه باشید!
انواع تجهیزات ابزار دقیق و اتوماسیون بر حسب کاربرد
- ترموکوپل
- ترانسمیتر دما
- ترانسمیتر فشار
- پرشر سوئیچ
- سنسور فشار مذاب
- سطح سنج
- فلومتر
- دتکتور گازی
- شیر یا ولو
- سنسور پراکسیمیتی
حال که با مهمترین انواع این ابزار ها در صنعت آشنا شدیم، شاید برایتان سوال باشد که معروفترین و پرکاربردترین تجهیزات ابزار دقیق کدامند؟ بدلیل گستردگی متغیرها و تکنولوژی و ابزارهای مختلف موجود برای اندازه گیری هرکدام از آنها، دسته بندی یکجای تمامی این وسایل بسیار دشوار خواهد بود؛ ولی ما در آداک فرآیند سپهر پرکاربردترین ابزارهای دقیق را در ادامه بزبان ساده به شما خواهیم گفت تا با کارکرد هرکدام آشنا شوید!
مهمترین تجهیزات اندازه گیری دما
دما یکی از مهمترین متغیرهایی است که در صنعت بایستی بطور دائم تحت نظارت بوده و مقادیر آن در رنج نرمال نگه داشته شود. بسته به موارد مختلفی مانند شرایط محیط و نیز دمای مدنظر میتوان برای اندازه گیری دما از تجهیزات مختلفی استفاده نمود. چند نمونه از این تجهیزات اندازهگیری دما را با هم بررسی میکنیم.
ترموکوپل Thermocouple
ترموکوپلها از پرکاربردترین سنسورها برای اندازه گیری دما هستند. ترموکوپل ها از نوع غیرتماسی بوده و میتوانند رنج وسیعی از دماها را اندازه گیری کنند. ترموکوپل ها دارای تیپهای مختلفی هستند؛ مثلا انواع R – S – B دارای قابلیت اندازهگیری دما در محدوده (۲۰۰-) الی (۱۸۰۰) بوده و انواع L – K- J قابلیت اندازهگیری دما در محدوده (۱۸۰-) الی (۱۰۰۰) درجه سلسیوس را دارند. همانطور که میبینید، هر کدام از تیپها میتوانند دما را در بازه مشخصی اندازه گیری کنند.
از معایب ترموکوپلها میتوان به غیرخطی بودن خروجی آنها نسبت به دما اشاره کرد. اما این موضوع به چه معناست؟ تصور کنید که تفاوت ولتاژ خروجی ترموکوپل در دمای 100 و 200 درجه سلسیوس برابر 0/1 ولت باشد. این تفاوت در ولتاژ بین دمای 1000 و 1100 بسیار کمتر از 0/1 ولت خواهد بود. بعبارتی نمودار خروجی نسبت به دما در ترموکوپلها بشکل خطی نبوده و حالت لگاریتمی دارد. به همین خاطر، برای نظارت دقیق استفاده از کالیبراتور در اولویت است.
ترانسمیتر دما Temperature Transmitters
ترانسمیترهای دما نیز از دسته پرکاربرد تجهیزات ابزار دقیق هستند که وظیفه تبدیل سیگنالهای الکتریکی از ترموکوپل را به سیگنال استاندارد را برعهده دارند. همانطور که میدانید، سیگنال خروجی از ترموکوپل در حد میلی ولت بوده و به هیچوجه برای انتقال مناسب نیستند.
ترانسمیترهای دما میتوانند این مشکل را حل کنند. ترانسمیتر دما میتواند بصورت دو سیمه، سه سیم و چهار سیم عمل کند. در حالت دو سیم، ترانسمیتر دارای دو سیم خروجی است که یک سیم آن به پایه منفی منبع تغذیه و سیم دیگر به دستگاه کنترلی متصل میشود. در حالت سه سیمه، یک سیم آن با سیم منفی منبع تغذیه و سیم دیگر با سیم مثبت منبع تغذیه و سیم دیگر به دستگاه کنترلی متصل میشود. در حالت چهار سیمه، دو سیم خروجی به سیم منبع تغذیه و دو سیم دیگر به دستگاه کنترلی متصل میشود.
این دستگاهها معمولاً دارای ورودی سنسور دمایی مانند رزیستانس دما، ترموکوپل یا ترمیستور هستند و سیگنال خروجی آنها بشکل سیگنال جریان یا ولتاژ است که باید به سیگنال استاندارد مانند 4 الی 20 میلی آمپر یا 10-0 ولت تبدیل شود. ترانسمیتر دما علاوه بر تبدیل سیگنال دما به سیگنال استاندارد، امکانات دیگری نیز دارد که میتوان به: تنظیم محدوده خروجی، امکان کالیبراسیون، تشخیص خطا و تعیین مقدار حداکثر و حداقل دما اشاره کرد.با استفاده از ترانسمیتر دما، دقت اندازهگیری دما افزایش مییابد و در نتیجه، کنترل و نظارت بر فرآیندهای صنعتی بهبود مییابد.
همچنین، با استفاده از ترانسمیتر دما، مشکلاتی مانند تداخل الکترومغناطیسی و تاثیر تغییرات دما در سیستم کنترل کاهش مییابد. ترانسمیتر دما میتواند بحالت آنالوگ یا دیجیتال عمل کند. در حالت آنالوگ، سیگنال خروجی میتواند ولتاژی یا جریانی با مقدار متناسب با دمای اندازهگیری شده باشد. در حالت دیجیتال، سیگنال خروجی بصورت دیجیتال با استفاده از پروتکلهایی مانند HART، FOUNDATION Fieldbus، PROFIBUS PA و یا MODBUS RTU ارسال میشود.
ترانسمیتر دما میتواند بعنوان یک ابزار مهم در بسیاری از صنایع استفاده شود، از جمله صنایع نفت و گاز، پتروشیمی، صنایع غذایی، صنایع دارویی و غیره. یکی از شناختهشدهترین برندها در زمینه تولید ترانسمیترهای دما، برند PR است که از شهرت جهانی در این زمینه برخوردار است.
فشار یکی دیگر از متغیرهای مهم در صنعت است. برخی از این تجهیزات برای اندازهگیری فشار در یک مخزن کاربرد دارند. همانطور که میدانید، اندازهگیری فشار در جامدات مفهوم ندارد، بنابراین از این نوع ترانسمیترها در مخازنی استفاده میشود که دارای گاز، بخار، مایع و یا مخلوطی از این موارد باشند. در ادامه مهمترین انواع ترانسمیترهای فشار را بررسی خواهیم نمود.
پرشر ترانسمیتر (ترانسمیتر فشار) Pressure Transmitter
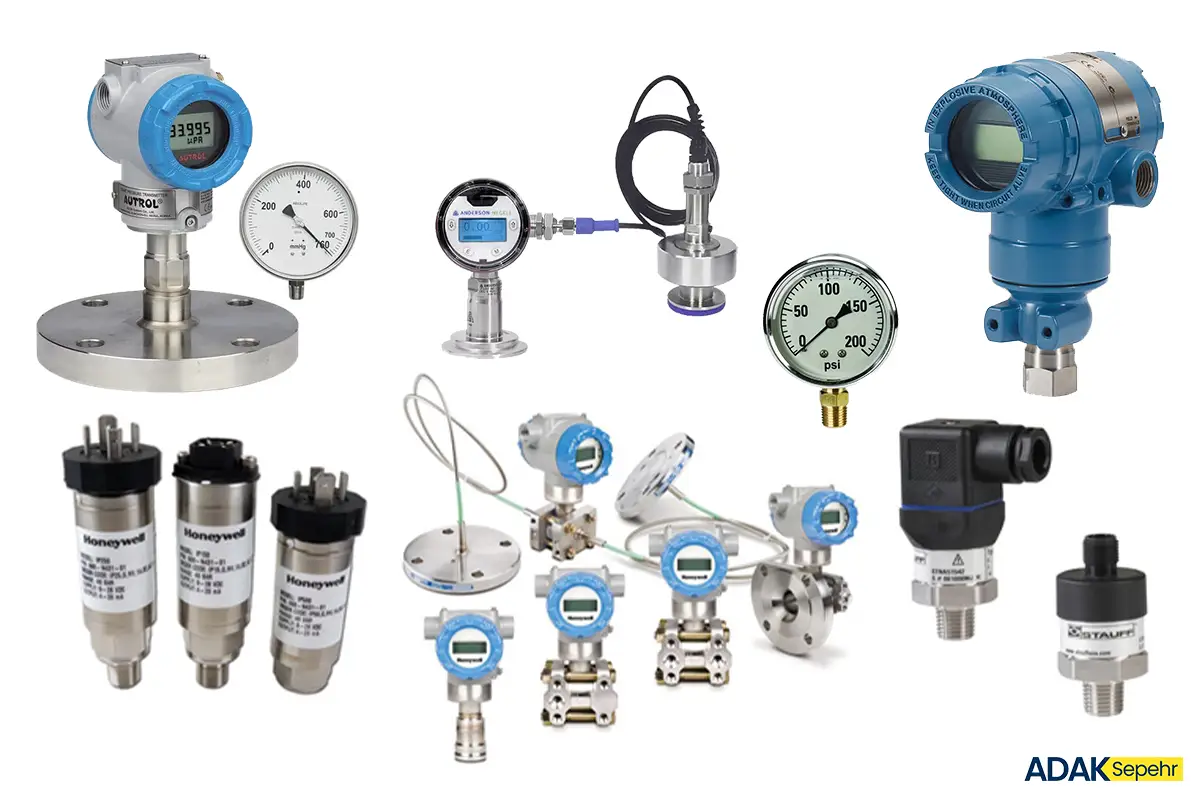
ترانسمیترهای فشار دقیق ترین و مهمترین ابزارهای موجود برای اندازهگیری فشار هستند؛ بهمین دلیل معمولا در جاهایی مورد استفاده قرار میگیرند که اندازهگیری دقیق فشار از اهمیت خاصی برخوردار است. پرشر ترانسمیترها از جمله پراستفادهترین تجهیزات در صنایع پتروشیمی و پالایشگاهی هستند. استفاده از ترانسمیتر فشار در مخازن LPG بسیار ضروری است تا حد فشار درون مخزن همیشه در سطح نرمال باقی بماند.
مهمترین سنسورهای فشار عبارتند از:
- سنسور فشار پیزو مقاومتی: فشار سبب اعمال نیرو به حسگر شده و مقدار مقاومت آن تغییر مییابد. با استفاده از این تغییر، مقدار فشار موجود اندازه گیری میشود. این نوع از حسگرها دارای حساسیت، استحکام و نیز مقاومت حرارتی بالایی بوده و سیگنال خروجی کمی دارند.
- سنسور فشار پیزو الکتریکی: با وارد شدن فشار بر سطح سنسور فشار پیزو الکتریک یک سیگنال ضعیف ولتاژی در خروجی سنسور ایجاد میشود. معمولا سنسور فشار پیزو الکتریک از کریستالهای طبیعی مانند تورمالین یا کوارتز ساخته میشود. خروجی سنسورهای پیزو الکتریک تقریبا خطی بوده، رنج تحمل فشار در پیزو الکتریک بین 0.07 بار الی 70 بار دقت نیز در حدود 0.1 میباشد.
- سنسور فشار خازنی: دیافراگم در این حسگر یکی از صفحات خازن است. با تحت فشار قرار گرفتن دیافراگم حالت آن و در نتیجه ظرفیت خازن نیز تغییر میکند. دقت و حساسیت این سنسورها بسیار بالا بوده و در صورت قرار گرفتن در معرض لرزش بدرستی عمل نمیکنند.
برای استعلام قیمت سنسور فشار کلیک کنید!
برند وگا (VEGA) آلمان یکی از بهترین سازندگان تجهیزات ابزار دقیق برای اندازه گیری فشار است. با آداک فرآیند سپهر شما میتوانید بصورت بدون واسطه، با کمترین قیمت و نیز گارانتی تجهیز موردنیازتان را از وگا آلمان خرید نمایید؛ آن هم با قابلیت استعلام اصالت از وبسایت وگا!
ترانسمیتر فشار قلمی
ترانسمیتر فشار قلمی یک راه حل سادهتر و بسیار ارزانتر برای اندازه گیری فشار است. ترانسمیترهای فشار قلمی همانطور که از نامشان پیداست، اندازهای بسیار کوچکتر و قیمتی بمراتب ارزانتر نسبت به ترانسمیترهای فشار معمولی دارند. این نوع از ترانسمیترهای فشار در مواقعی بکار میروند که فشار موردنظر بسیار بالا نبوده و از طرفی، اندازهگیری کاملا دقیق هم مدنظر نباشد. مثلا در کمپرسورها و یا جکهای هیدرولیک، معمولا از ترانسمیترهای فشار قلمی استفاده میشود.
سنسور فشار مذاب Melt Pressure
از این سنسورها بیشتر در صنایع تزریق پلاستیک استفاده میشود. در دستگاه تزریق پلاستیک اگر فشار داخل بخش اکسترودر از مقدار معینی بیشتر باشد، محصول دارای ضخامت بیش از حد بوده و در صورتی که فشار از حد معینی کمتر باشد، محصول دارای ضخامت کمتر از حد نرمال خواهد بود. از همین رو، در این صنایع کنترل فشار مواد مذاب درون اکسترودر از اهمیت بسیاری برخوردار است.
دمای داخل مخزن اکسترودر بسیار بالا بوده و همچنین دارای مواد مذاب هستند. بنابراین، برای کنترل فشار مواد مذاب در اکسترودر، از نوعی حسگر فشار به نام سنسور فشار مذاب یا همان Melt استفاده میشود. سنسور فشار مذاب در دو نوع موجود است؛ با ترموکوپل و بدون ترموکوپل. در نوع دارای ترموکوپل، سنسور همزمان فشار و دما را باهم اندازهگیری میکند در صورتی که در نوع بدون ترموکوپل صرفا فشار اندازه گیری خواهد شد.
تجهیزات ابزار دقیق برای اندازه گیری سطح Levels of Measurement
سطح سنجها دستهای بسیار مهم از تجهیزات ابزار دقیق هستند که برای اندازهگیری ارتفاع مواد موجود درون یک مخزن و یا چاه استفاده میشوند. سطح سنجها از لحاظ نوع عملکرد، کاربرد و نیز تکنولوژی بکار رفته بسیار متنوع بوده و هرکدام در شرایط و محیط های خاصی استفاده میشوند. برای همین قبل از هر اقدامی در زمینه تهیه ابزارهای اندازهگیری سطح، بایستی اطمینان حاصل نمود که تجهیز میتواند در آن مخزن بخصوص عمل نماید. سطح سنج چیست و جادوی آن چگونه اتفاق می افتد؟
تجهیزات اندازهگیری سطح نقش عمدهای در ایجاد اتوماسیون دارند. مثلا میتوان با استفاده از لول ترانسمیترها، برای هر مرحله از پر شدن مخزن یک عمل خاص برنامه ریزی نمود.
مثلا در نظر بگیرید که یک مخزن باید تا حد معینی با آب پر شود، سپس یک ماده پودری به آن اضافه شده و میکسر شروع بکار کند. تجهیزات ابزار دقیق اندازهگیری سطح، تمامی این موارد را ممکن میسازند. البته، در مثال بیان شده باید از تجهیزی استفاده شود که قابلیت تشخیص سطح مایعات و جامدات را بشکل همزمان داشته باشد.
ابزار های اندازهگیری سطح عمدتا شامل لول سوئیچها و لول ترانسمیترها هستند. لول سوئیچها برای تشخیص نقطهای سطح و لول ترانسمیترها برای تشخیص پیوسته استفاده میشوند. در ادامه انواع سطح سنج ها را بررسی میکنیم.
لول ترانسمیتر Level Transmitters
همانطور که گفته شد، لول ترانسمیترها از تجهیزات ابزار دقیق هستند که برای اندازه گیری پیوسته سطح بکار میروند. بیشتر لول ترانسمیترها خروجی استاندارد 4-20 میلی آمپری دارند که با استفاده از این روش میتوانند ارتفاع دقیق مواد درون مخزن و یا چاه را گزارش دهند. ترانسمیترهای سطح بیشتر براساس تکنولوژی امواج عمل میکنند و شامل لول ترانسمیترهای راداری و التراسونیک هستند.
لول ترانسمیترهای راداری از امواج الکترومغناطیسی استفاده میکنند و بنابراین میتوانند حتی در شرایط خلا هم سطح مواد را تشخیص دهند؛ در صورتی که لول ترانسمیترهای التراسونیک بخاطر استفاده از امواج مکانیکی این قابلیت را ندارند.
لول سوئیچ LEVEL SWITCH
بزبان ساده، لول سوئیچ ها میتوانند حضور و یا عدم حضور ماده درون مخزن در یک سطح خاص را تشخیص دهند. لول سوئیچها در نقاط خاصی از مخزن نصب میشوند و میتوانند گزارش دهند که آیا سطح مواد از این نقطه بالاتر است یا خیر.
سوئیچهای سطح انواع مختلفی دارند که هرکدام برای شرایط خاصی مناسبترند. این دسته از ابزارهای دقیق شامل لول سوئیچ های خازنی و دیاپازونی میشوند. البته انواعی از لول سوئیچها با فناوری قدیمی تر نیز وجود دارند. این تجهیزات معمولاً در صنایع شیمیایی، نفت و گاز، پتروشیمی، آب و فاضلاب، خودروسازی و صنایع مشابه استفاده میشوند.
لول سوئیچ ها از لحاظ خروجی به دو دسته تقسیم میشوند: آنالوگ و دیجیتال. در سوئیچهای آنالوگ، سنسوری که در محیط مواد قرار دارد، با توجه به تغییرات سطح، سیگنالی آنالوگ تولید میکند که بعنوان ورودی به یک مدار الکترونیکی داده میشوند. در سوئیچهای دیجیتال، سطح مواد، بصورت دیجیتال تشخیص داده میشود. این سوئیچها اغلب قابلیت تنظیم سطح تشخیص داده شده را دارند و در صورت برخورد با سطح ماده، یک سیگنال دیجیتال تولید میکنند که به سیستم کنترل دستگاهی که در آن قرار دارند، داده میشود.
قیمت و خرید لول سوئیچ
در کاربردهای صنعتی، لول سوئیچها معمولاً برای کنترل سطح مایعات و جامدات در مخازن، تانکها، سیستمهای تبرید و سیستمهای خنککننده مورد استفاده قرار میگیرند. همچنین، این تجهیزات میتوانند به عنوان ابزارهای ایمنی در صنایع شیمیایی و پتروشیمی به کار گرفته شوند.
فلومتر Flowmeter
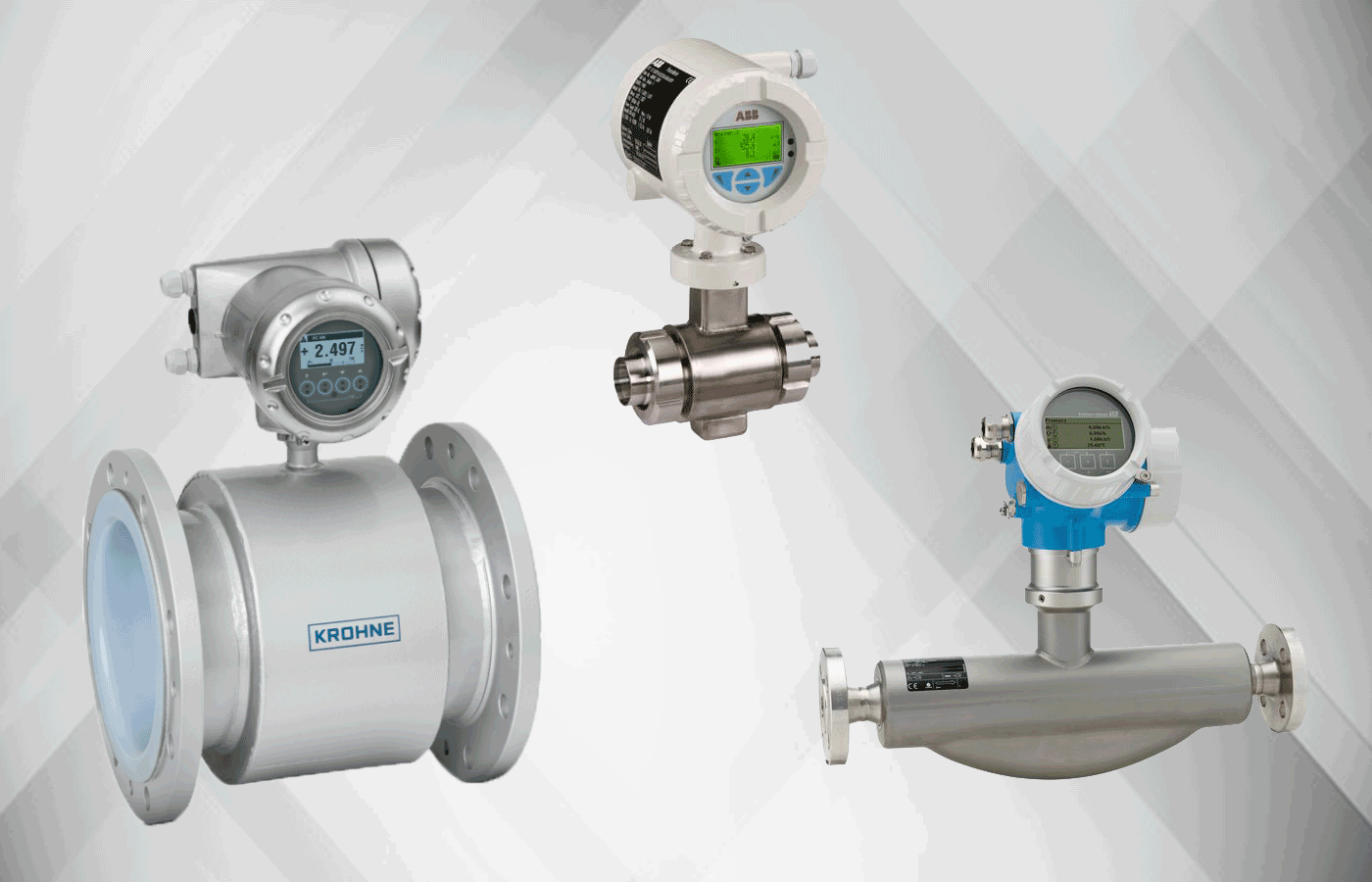
چند نمونه فلومتر
بسیاری از مواقع، اینکه در واحد زمان چه مقدار ماده از یک مقطع عبور میکند، برای ما اهمیت خاصی دارد. این اندازهگیری میتواند به دو صورت انجام گیرد: حجم ماده عبوری از مقطع در واحد زمان و یا جرم مواد عبوری (به ترتیب دبی حجمی و دبی جرمی).
برای اندازهگیری حجم و یا جرم مواد عبوری نسبت به واحد زمان، از فلومترها استفاده میکنیم. فلومترهای جرمی با پیشوند Mass اغاز شده و مقدار فلو را نسبت به جرم سیال میسنجند. انواع مختلفی از فلومترها بر حسب نوع عملکرد وجود دارند و در صنعت مورد استفاده قرار میگیرند؛ مانند فلومترهای مغناطیسی، فلومتر ورتکس، فلومتر کوریولیس، فلومتر التراسونیک و روتامتر.
بهترین برند تجهیزات ابزار دقیق برای اندازه گیری فشار و سطح
وگا (VEGA)، اندرس هاورز (Endress+Hauser) و رزمونت (Rosemount) از مهمترین تولیدکنندگان تجهیزات ابزار دقیق هستند که برای اندازهگیری فشار و ارتفاع مواد درون مخزن و چاهها بکار میروند. اما ما در آداک فرآیند سپهر، برند وگا را به مدیران و تولیدکنندگان حرفهای پیشنهاد میدهیم. اما آیا این موضوع صرفا یک اعتقاد شخصی است؟ به هیچ وجه!
اولین دلیل بهترین بودن وگا، به سیاستهای این شرکت برمیگردد. در حالی که دیگر برندها مانند اندرس هاوزر و یا رزمونت (امرسون) ترجیح میدهند بسیاری از قطعات تجهیزات خود را در کشورهای ثالت تولید کنند، جزء به جزء محصولات برند وگا در شرکت مادر در آلمان تولید میشود.
اینکه تجهیز تولید شده در آلمان در مقایسه با تجهیزات تولید شده در کشورهای ثالث نظیر چین و هند چقدر از لحاظ کیفیت، دقت و طول عمر بهتر است، تنها یک وجه ماجراست که باید در نظر بگیریم. یک مزیت دیگر این موضوع، این است که چون در تجهیزات وگا تمامی فرآیند تولید در شرکت مادر انجام میشود، فرآیند تولید و تحویل تجهیز به مصرف کننده کاملا یکپارچه است. اما این موضوع به چه معناست؟
بعلت یکپارچگی تولید و فروش در سنسور های برند وگا، شما با استفاده از شماره سریال درج شده روی تجهیز براحتی میتوانید ببینید که در چه تاریخی تولید شده، مشخصات دقیق آن چه بوده و مهمتر از همه، تاریخ تست تجهیز چه زمانی بوده است! خوب این موضوع چرا باید اهمیت داشته باشد؟
متاسفانه بخاطر محدودیتها و شرایط تامین کالا در صنعت ایران، در بسیاری از موارد مشاهده میشود که برخی تامین کنندگان کالاهای استوک و تعمیری را بعنوان تجهیز نو به مشتری تحویل میدهند. بخاطر ارائه شدن مشخصات دقیق و نیز تاریخ تست، این موضوع در وگا بسادگی تمام قابل تشخیص است، اما در برندهای دیگر خیر!
دتکتور گاز Gas Detector
دتکتور گاز، تجهیز ابزار دقیقی است برای شناسایی و اندازه گیری گازهایی که برای انسان خطرناک هستند. این دسته از گازها شامل گازهای قابل اشتعال و انفجار، سمی، اسیدی و یا اکسید کننده هستند. دتکتورهای گاز در صنایع شیمیایی و پتروشیمی استفاده بسیار گسترده ای دارند و جزو مهمترین تجهیزات ابزار دقیق بشمار میروند. دتکتورهای گاز در دو نوع ثابت و پرتابل (قابل حمل) به بازار عرضه می گردد.
دتکتورهای گاز ثابت برای صنایعی کاربرد دارند که اندازهگیری پیوسته وجود یا عدم وجود یک گاز در محیط همواره اهمیت دارد. مثلا در صنایع شیمیایی، معمولا از دتکتورهای گاز کلر استفاده میشود. همانطور که میدانید، گاز کلر بسیار سمی و کشنده است و پایش پیوسته آن در محیط اهمیت بسیاری دارد. در مقابل، از دتکتورهای گاز پرتابل به مانند وسایل فردی و یا اندازهگیری غلظت یک گاز خاص در مواقع خاص و یا چکاپها استفاده میشود.
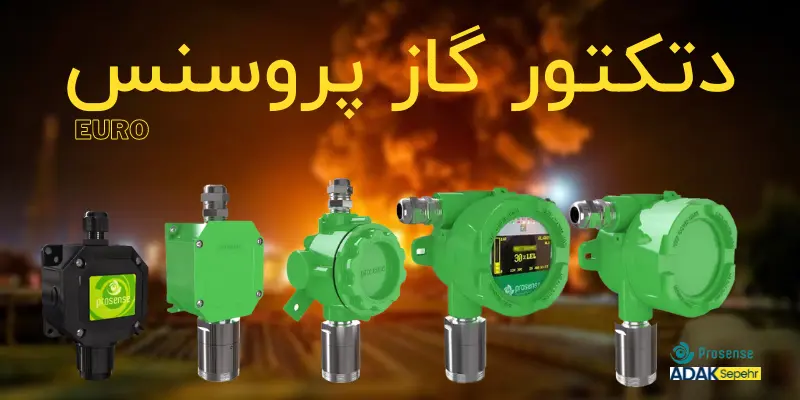
بهترین برند دتکتورهای گاز
هانیول (Honeywell)، درگر (Dräger)، پروسنس (Prosense)، کروکان (Crowcon) و اماسآ (MSA) از جمله شناختهشدهترین برندهای تجهیزات ابزاردقیق دتکتور در سطح جهان هستند؛ بنحوی که تنها در سال 2019، این پنج برند بیش از 65 درصد دتکتورهای گاز ثابت و پرتابل جهان را تامین کردند.
بدیهی است که قبضه کردن این بازار توسط این برندها، به هیچ وجه اتفاقی نیست! بجرأت میتوان گفت تجهیزات این پنج برند در زمینه دتکتورهای گازی، از جنبههایی مانند امکانات، قابلیت اطمینان و طول عمر یک سر و گردن بالاتر از دیگر برندهاست.
خوشبختانه در صنعت ایران نیز دقیقا وضع مشابه بازار جهانی است؛ بطوری که اکثریت شرکتها و تولیدیهای معتبر، از محصولات این برندها استفاده میکنند. اما از طرفی، صنعت ایران نیز شرایط و مقتضیات خاص خود را دارد. با در نظر گرفتن این مورد، بیایید مقایسه را حتی سختتر کنیم: کدام یک از این برندها بهترین است؟
برای اطلاع از قیمت و انواع دتکتور گاز کلیک کنید!
خبر خوش این است که ما قبلا تمامی این موارد را برای شما لیست کرده و بهترین برند در این زمینه را معرفی کردهایم، کافی است فقط مقاله بهترین برند دتکتورهای گاز در ایران کدام برندها هستند؟را بخوانید!
ولو Valve یا شیر در ابزار دقیق
از لحاظ ساختار نیز شیر کنترلی صنعتی در دو نوع: دارای حرکت خطی و دورانی تولید شدهاند.
انواع شیر کنترلی
- ON/OFF ولوها (بال ولو Ball Valve و باترفلای ولو Butter Fly Valve از این نوع هستند)
- شیر ایمنی Safety valve
- شیر ایزوله (شیرهای اسپلیت، شیر های تک نشیمنگاه یا سینگل سیت Single Seat و شیر چاقویی Knife Valve از شیرهای ایزوله محسوب میشوند)
- شیر های کنترل Control Valve (گلوب ولو Globe Valve و شیر سوزنی Needle valve)
- شیرهای خود کنترل یا چک ولو Check Valve
- شیر دروازه ای Gate valve
- شیر دیافراگمی Diaphragm valve
- شیر کشویی Slide valve
- شیر برقی Solenoid valve
- شیر تنظیم فشار برگشتی Back pressure regulating valve و شیر تنظیم جریان Flow regulating valve
- Flush bottom valve
پوزیشنر Positioner
پوزیشنر (Positioner) یک دستگاه کنترلی و یکی از اجزای حیاتی سیستم های ابزار دقیق است، و علت استفاده از آن در مکانیزمهای صنعتی کنترل دقیق شیر (Valve) و کمپرسورها (Compressor) برحسب نیاز کاربر است. در کاربردهای صنعتی، پوزیشنرها بصورت گسترده در صنایع نفت و گاز، پتروشیمی، نیروگاهی، کوره ها، صنایع شیشه قسمت لهر، آب و فاضلاب، نیروگاهها و صنایع معدنی مورد استفاده قرار میگیرند.
پوزیشنر ها بر روی اکچویتور نصب می شوند و با انجام عملیات کاهش و یا افزایش، شیر را در وضعیت درست و مناسب قرار می دهند. و در چهار نوع نوع: آنالوگی، دیجیتالی، پنوماتیکی و موتور دار ساخته میشوند.
این دستگاهها برای اندازهگیری و نظارت بر ولتاژ و جریان الکتریکی در سیستمها و تجهیزات مختلف استفاده میشوند.
سنسور مجاورتی Proximity Sensor در ابزار دقیق
حسگرهای پراکسیمیتی از تجهیزات ابزاردقیق هستند که وجود اجسام را در فاصله معینی از خود تشخیص میدهند. نکته مهم در این سنسورها این است که آنها از روش غیر تماسی برای تشخیص اشیا استفاده میکنند. سنسورهای مجاورتی در اشکال و اندازه های بسیار متنوعی وجود دارند. انواع سنسورهای مجاورتی عبارتند از، سنسور القایی، سنسور خازنی، سنسور التراسونیک و سنسور نوری.
ifm – omron – Pepperl+Fuchs – Autonics – TURCK برند ها و کمپانی های مطرح در زمینه تولید سنسور مجاورتی هستند.
انواع سنسور های پراکسیمیتی
سنسور پراکسیمیتی القایی Inductive Proximity Sensors
این حسگرها برای تشخیص اجسام فلزی بر اساس اصل اندوکتانس کار میکنند. هنگامی که یک جسم فلزی نزدیک سنسور میشود، جریان های گردابی ایجاد شده سنسور، توسط جسم جذب شده و در نتیجه شدت میدان نوسانی سنسور تغییر میکند. از مزایای سنسور القایی، دقت فوق العاده، نرخ سوئیچینگ بسیار بالا و قابل نصب در اکثر محیط های صنعتی اشاره کرد.
سنسور خازنی Capacitive Proximity Sensor
آنها برای تشخیص اجسام فلزی و همچنین غیرفلزی از جمله مایعات و خمیرها استفاده می شوند و بر اساس اصل ظرفیت خازن کار میکنند. صفحه داخل حسگر بعنوان یک صفحه خازن و سطح جسمی که باید شناسایی شود بمنزله صفحه دیگری از آشکارساز عمل می کند. محیط مادی (عموما هوا) بین آنها مانند دی الکتریک عمل می کند. هنگامی که جسم به سنسور نزدیکتر می شود ظرفیت خازن افزایش می یابد و اگر جسم از سنسور دور شود ظرفیت خازن کاهش می یابد. از مزایای این سنسور ها، هزینه نسبتاً پایین و سرعت بالا اشاره کرد.
سنسور فتوالکتریک
این سنسور ها برای تشخیص اجسام از پرتو نور استفاده میکنند. دو بخش اصلی این سنسور ها شامل فرستنده و گیرنده است که فرستنده برای انتشار پرتو نور و گیرنده برای دریافت نور. از مزایای سنسور فتوالکتریک (حسگر نوری) به دامنه بسیار وسیع و ایمن بودن در برابر تأثیرات الکتریکی یا مغناطیسی اشاره کرد. و از معایب این سنسورها، تحت تأثیر اثرات محیطی مانند گرد و غبار، باران و غیره قرار گرفتن است.
سنسور مجاورتی التراسونیک Ultrasonic Proximity Sensor
پراکسیمیتیهای التراسونیک از امواج صوتی برای تشخیص اجسام استفاده میکنند.این سنسور ها دارای فرستنده و گیرنده هستند. این سنسور ها تحت تأثیر اثرات محیطی مانند گرد و غبار، باران و غیره قرار نمی گیرند و همچنین می توانند در شرایط بسیار نامطلوب مورد استفاده قرار گیرند. اما سنسور های التراسونیک امکان استفاده در خلاء یا زیر آب نیستند.
میرایی در تجهیزات ابزار دقیق
یک ترانسمیتر معمولا تغییرات جریان، دما ، فشار و سطح را در ورودی تجهیز اندازه گیری میکند و در خروجی ترانسمیتر سیگنال استاندارد برحسب نوع سنسور ایجاد میشود. این تغییرات را متغییر ورودی میگوییم. قطعا آن ترانسمیتر یک لول ترانسمتر سطح باشد یا پرشر ترانسمیتر.
بیشتر تجهیزات ابزاردقیق دارای سنسوری هستند که متغیر ورودی را اندازه گیری می کند و خروجی مشترکی بین 4 تا 20 متر آمپر (سیگنال استاندارد) ارائه میدهد.
مفهومی بنام میرایی در عملکرد ترانسمیتر ها از اهمیت بسیار بالایی برخوردار است. خروجی فرستنده باید بروز شده و مطابق با تغییرات ورودی، تغییر کند.
میرائی چیست؟
میرایی عبارت است از مدت زمان مورد نیاز برای رسیدن به 63.2 درصد از ارزش نهایی ترانسمیتر پس از اعمال مرحله تغییر در ورودی، علاوه بر زمان بروز رسانی.
میرایی ترانسمیترها را می توان از 1 تا 32 ثانیه تنظیم کرد. میرایی تاثیرات نویز الکتریکی و هرگونه نویز موقتی ناچیز دیگری را که روی سیگنال خروجی ترنسمیتر تأثیر بگذارد، کاهش می دهد. اغلب برای تثبیت حلقه کنترل و جلوگیری از مقادیر اشتباه استفاده می شود.
مثالهایی از کاربرد ابزار دقیق عبارتاند از:
- استفاده از ترمومترها برای اندازهگیری دما در یک فرآیند صنعتی.
- استفاده از فشارسنجها برای نظارت بر فشار در یک مخزن گاز.
- استفاده از ولتمترها و آمپرمترها برای اندازهگیری ولتاژ و جریان در یک سیستم الکتریکی.
- استفاده از آنالایزرهای شیمیایی برای تحلیل ترکیبات شیمیایی در نمونههای آزمایشگاهی.
کار ابزار دقیق برای کنترل فرآیندها، تضمین کیفیت محصولات، ایمنی صنعتی و اطلاعات دقیق در تحقیقات و توسعه بسیار اهمیت دارد.
ابزار دقیق برق صنعتی چیست؟
ابزارهای دقیق برق صنعتی، وسایلی هستند که برای اندازهگیری، کنترل و نظارت بر پارامترهای برقی در محیطهای صنعتی بکار میروند. این ابزارها بدلیل اهمیت بالایی که دارند، نقش بسیار مهمی در بهبود عملکرد و کارایی فرآیندهای صنعتی ایفا میکنند.
با استفاده از این ابزارها، امکان اندازهگیری دقیق و کنترل بهینه بر پارامترهای برقی، مانند ولتاژ، جریان، فرکانس و قدرت، در فرآیندهای صنعتی بوجود میآید. در ادامه انواع تجهیزات برق صنعتی را نام میبریم.
انواع تجهیزات برق صنعتی
- انواع کلیدها (کلید کامپکت – کلید هوایی – کلید تابلویی)
- درایوهای DC – اینورتر AC و سافت استارتر
- تابلو برق – سینی – داکت و چراغ سیگنال
- رله ضربهای – رله شیشهای و رله فالت
- انواع کابل فشار قوی و فشار ضعیف
- رله حفاظت موتور و کنترل فاز
- ترانسهای کاهنده و افزاینده
- مولتیمتر – واتمتر و آمپرمتر
- فیوز فشنگی و منیاتوری
- تجهیزات هشدار و آژیر
- انواع ترمینال تابلویی
- رگلاتور و بانک خازنی
- کنتاکتور و بیمتال
- موتور و پمپ
مهمترین تولید کنندگان تجهیزات ابزار دقیق و اتوماسیون در سطح جهان کدامند؟
شرکتهای بسیاری هستند که در زمینه تولید این تجهیزات فعالیت دارند. چند نمونه از مهمترین تولیدکنندگان جهانی تجهیزات ابزار دقیق عبارتند از:
وگا (VEGA)، اندرس هاوزر (E+H)، زیمنس (Siemens) و درگر (Dräger) آلمان، هانیول (Honeywell) آمریکا، پروسنس (Prosense) ترکیه، اشنایدر (Schneider)، UWT آلمان ، پپرل اند فوکس (Pepperl Fuchs)، ویکا (WIKA)، نووس (NOVUS)، ایبیبی (ABB)، زیکا (SIKA)، وایدمولر (Weidmüller)، پیلز (Pilz)، شمرسال (Schmersal)، فونیکس (PHOENIX CONTACT)، میکرو دتکتور (Micro Detectors)، امرون (OMRON)، یوشیتاکه (Yoshitake)، یوکوگاوا (Yokogawa) و یاسکاوا (Yaskawa) ژاپن، اپکس (Apex)، فستو (Festo)، آی اف ام (ifm)، رکس روث (Rexroth) و Lenze.
بیشتر این برندها بر ساخت تجهیزات خاصی متمرکز هستند؛ مثلا شرکتهای وگا و اندرس هاوزر بیشتر در زمینه سنسورهای سطح و نیز سنسورهای فشار متمرکز هستند. بهمین دلیل، زمانی که پای مقایسه به میان بیاید، بهتر است هرکدام از این برندها را با برندهای متناسب مقایسه کنیم.
مشاوره در زمینه تجهیزات ابزار دقیق
ما در این مطلب تلاش کردیم تا به تمامی سوالات شما در زمینه ابزارهای دقیق پاسخ دهیم؛ اما ممکن است هنوز سوالاتی در ذهن شما باشد که بیجواب ماندهاند. واحد مشاوره شرکت آداک فرآیند سپهر بعنوان بزرگترین تامین کننده تجهیزات ابزاردقیق برند وگا، پروسنس و اتک در ایران دقیقا برای همین منظور اینجاست!
آداک فرایند سپهر با تعهد به ارائهی بهترین تجهیزات ابزار دقیق و بروزترین فناوریها، نقش بسیار مهمی در پیشرفت و بهبود صنایع ایران ایفا میکند. اگر به تجهیز خاصی نیاز داشته باشید، براحتی با ما تماس بگیرید، مشاوره رایگان دریافت و تجهیز موردنظر را با گارانتی، بهترین قیمت و ضمانت اصالت خرید کنید. همچنین میتوانید با تکمیل فرمهای کوتاه درخواست مشاوره برای ابزار های موردنیازتان، در ساعت و تاریخ مدنظر خودتان مشاوره 100% رایگان دریافت کنید!
اگر نظر و یا پیشنهادی دارید، لطفا در بخش نظرات با ما در میان بگذارید. از اینکه در این مطلب از وبسایت آداک فرآیند سپهر با ما همراه بودید، سپاسگزاریم!
سوالات متداول
انواع تجهیزات ابزاردقیق و موارد استفاده در صنایع و کارخانجات کدامند؟
با توجه به نیاز کارخانجات صنعتی دستگاه های ابزار دقیق شامل: سنسور های تشخیص سطح و کالا، لودسل، فلومتر، ترانسمیتر ها، کنترلرها، ترموکوپل، ولوهای برقی و مکانیکال، پرشر ترانسمیتر و پرشر سوئیچ ها، ترانسدیوسر، دتکتور گاز، رکوردر و نمایشگرها میشوند.
سیگنال خروجی استاندارد در ابزار دقیق چیست؟
دستگاههای مختلف ابزاردقیق بعد از عمل اندازهگیری کمیّتهای فیزیکی مثل: دما، فشار، وزن، جریان و سطح در خروجی خود سیگنال آنالوگ 4 الی 20 میلی آمپر تحویل میدهند. مفهوم جریان های زیر 4mA بمعنی خطا در تجهیز یا ایراد در کابل ارتباطی است. جریان 4mA بعنوان حداقل مقدار کمیت اندازهگیری شده و 20mA حداکثر آن کمیّت است.
کالیبراسیون سنسور های ابزار دقیق به چه صورت است؟
چون تنوع وسایل ابزار دقیق بسیار زیاد است بهمین دلیل هر نوع تجهیزی باید با توجه به دفترچه راهنمای کالیبراسیون خودش، که شرکت سازنده در اختیار شما قرار داده، توسط پرسنل مجرب انجام پذیرد. مثلا: مراحل کالیبره کردن سطح سنج با دتکتور گاز فرق دارد.
چرا خروجی اکثر سیستمهای ابزار دقیق سیگنال جریانی 4 الی 20 میلی آمپر است؟
سیگنال 20-4 (mA) نوعی حلقه جریان الکتریکی است که از آن در سیستم های کنترلی استفاده میشود. این سیگنال آنالوگ، کمتر مستعد نویز است و قادر است سیگنال صفر زنده (4mA بمعنای صفر) را ارائه دهد. که در آن 4 میلی آمپر کمترین مقدار قابل اندازه گیری، 20mA حداکثر و مقادیر کمتر از 4 میلی آمپر وجود خطا یا قطع شدن تجهیز را نشان میدهد.
PH متر چیست؟
یک pH متر فعالیت یون هیدروژن را در محلول های مبتنی بر آب اندازه گیری میکند. این ابزار از یک الکترود حساس به pH (از جنس شیشه) برای اندازه گیری اسیدی یا بازی بودن محلول استفاده مینماید. انواع PH متر عبارتند از: PH متر پرتابل، قلمی، دارای خروجی سیگنال، آزمایشگاهی و تابلویی ثابت.
تفاوت سیگنالهای آنالوگ و دیجیتال در چیست؟
سیگنالهای آنالوگ پیوسته هستند و در طول زمان به آرامی تغییر می کنند، در حالی که سیگنال های دیجیتال گسسته هستند و آنی تغییر میکنند. سیگنالهای آنالوگ میتوانند تعداد نامحدودی از مقادیر را در یک محدوده داشته باشند، در حالی که سیگنالهای دیجیتال تنها صفر یا یک هستند.
شیر کنترل پنوماتیکی چگونه کار میکند؟
ولو کنترل پنوماتیک با تبدیل سیگنال الکتریکی به سیگنال فشار هوا کار میکند. سپس از این فشار هوا برای فعال کردن جکها، دمپرها و بطور کلی کنترل جریان سیال در فرآیندها استفاده میشود.
برسی حلقه در ابزار دقیق چیست؟
بررسی حلقه در ابزار دقیق فرآیندی است که در آن عملکرد و اتصالات حلقههای کنترل تأیید میگردد. این کار برای اطمینان از عملکرد صحیح حلقه کنترل قبل از شروع فرآیند انجام میشود.
تفاوت سنسور با مبدل چیست؟
حسگر وسیله ای است که یک کمیت فیزیکی را تشخیص داده و سیگنالی بر حسب آن کیمیت تولید میکند. اما مبدل یک شکل از انرژی را بشکل دیگری تبدیل میکند. در برخی موارد، سنسور میتواند نوعی مبدل باشد، اما قطعا مبدلها سنسور نیستند.
سروو موتور چیست؟
به موتورهای با دقت زیاد، با قابلیت کنترل موقعیت زاویهای، کنترل سرعت و شتاب را موتورهای سروو میگویند. کاربرد این موتورها بیشتر در ماشین افزار CNC و رباتیک است. این تجهیزات از یک انکودر (Encoder) یا رمزگذار برای افزایش دقت استفاده میکند.
پوزیشنر پنوماتیکی چیست؟
پوزیشنر پنوماتیکی با دریافت سیگنال ورودی الکتریکی و تبدیل آن به سیگنال خروجی پنوماتیک متناسب کار میکند. کاربرد این دستگاه برای کنترل موقعیت یک ولو عملیاتی در اتوماسیون صنعتی و خطوط تولید است.
لودسل چیست و چگونه کار میکند؟
لودسل نوعی حسگر است که برای اندازه گیری نیرو یا وزن استفاده می شود. لودسلها مقدار نیروی فشار حاصل از وزن را به سیگنال الکتریکی تبدیل میکنند. لودسل برای تشخیص مقدار وزن به عنصر استرین گیج (Strain gauge) مجهز هستند. لودسلها در ترازوهای خانگی، تجاری و صنعتی کاربرد دارند.
رله چیست و چه وظیفهای در مدار الکتریکی دارد؟
رله یک کلید برقی است که با تحریک سیم پیچ داخلی وصل میشود. بعبارتی رله یک کلید الکترومغناطیسی است که توسط یک جریان الکتریکی نسبتاً کوچک کار میکند و قادر است جریان الکتریکی بسیار بزرگتری را قطع یا وصل کند.
منبع : ابزار دقیق
|
امتیاز مطلب : 0
|
تعداد امتیازدهندگان : 0
|
مجموع امتیاز : 0